Por favor, use este identificador para citar o enlazar este ítem:
http://hdl.handle.net/20.500.14076/23248
Título : | Estudio de investigación tecnológica para acondicionar los gases de escape de los hornos con el fin de mejorar la eficiencia de despolvorización de los actuales electrofiltros |
Autor : | Bellido Espinoza, Glenny Alberto |
Palabras clave : | Hornos;Gases de escape;Electrofiltros |
Fecha de publicación : | 1983 |
Editorial : | Universidad Nacional de Ingeniería |
Resumen : | Cemento Andino S.A., empresa dedicada a la fabricación de cemento en los tipos I, II y V de las especificaciones A.S.T.M.; está situada en la sierra central del país a 3,860 m.s.n.m. con una planta cuya capacidad instalada es de 480,000 TM/año de Clinker, el cual se produce por el proceso de vía seca en tres hornos rotatorios. La fábrica opera a plena capacidad. Descripción del proceso El proceso por vía seca para la fabricación del cemento podemos resumirlo en las siguientes etapas. 1.- Extracción del Material. - Se efectúa con los equipos de movimiento de tierras y consiste en la explotación racionalizada de las canteras de materias primas que son la de caliza, óxido de fierro y oxido de aluminio. La explotación se realiza en coordinación con el Dpto. químico, el cual determina la ley de los materiales a extraerse dependiendo de las necesidades de composición. 2.- Chancado Primario. - La materia prima extraída es llevada hacia la chancadora primaria de doble eje de martillos, en la cual se le reduce el tamaño hasta partículas de 12 mm de como máximo. El material triturado es llevado a las canchas de alimentación de los molinos de crudo a través de fajas transportadoras. 3.- Molienda y Secado de la Materia Prima. - El material en las canchas de alimentación se encuentra con una humedad que varía entre 8% y 13% de acuerdo con la época de la verano o invierno. Este material es alimentado a los molinos de crudo (dos molinos de bolas) a través de las balan zas dosificadoras en forma independiente. Molino de Crudo I.- El material a procesarse en este molino es previamente pasado por la Torre de Secado, la cual usa los gases generados en el horno I. Al material se le reduce la humedad en un 4 % en la torre y luego pasa a el molino, donde es secado y finamente molido usando para ello los gases de escape del horno II. Se tienen humedades del 0.5 % y una finura con 15 % de residuo para la mella 4,900 de las normas DIN, a la salida del proceso de molienda y secado. Los gases provenientes del horno II ingresan al molino a 325 °C aproximadamente y salen de el a 95 °C en promedio, son enviados luego al electro filtro del mismo horno (electrofiltro 1) para ser depurados en un 94 %, ya que los gases en su recorrido arrastran partículas de polvo muy finas de los sistemas de hornos y molino, luego de filtrado los gases son emitidos a la atmósfera. A la materia prima molida y seca se le denomina harina cruda o crudo y es conducida luego a los silos de homogenización por medio de canaletes neumáticas y elevadores de cangilones. Molino de Crudo II.- En este caso el material ingresa directamente de las canchas al molino a través de las balanzas dosificadoras. No existe torre de secado para este circuito, pero en los proyectos de la empresa a mediano plazo este considerada la instalación de una torre de secado para este molino. En el molino. se realiza también el secado y molienda del material, obteniéndose valores similares a los del caso anterior, para lo cual se usan los gases de escape del horno III, estos ingresan al molino a 330 °C y salen a 95 °C, en promedio, para luego ser enviados al electro filtro del horno III (electrofiltro 2) en donde se separan las partículas de polvo de los gases en un 99 %, el gas limpio es emitido a la atmósfera. El crudo obtenido luego del proceso de secado y molienda es transportado a los silos de homogenización. En ambos casos cuando los molinos son sometidos a sus paradas programadas semanales, los gases de los hornos deben pasar directamente a sus respectivos electrofiltros a la temperatura que salen del sistema de cada horno, en el orden de los 330 °C. Como veremos posteriormente estas altas temperaturas de operación para los electro-precipitadores hace que su eficiencia de filtrado baje sustancialmente, emitiéndose los gases a la atmósfera con altas concentraciones de polvo. |
URI : | http://hdl.handle.net/20.500.14076/23248 |
Derechos: | info:eu-repo/semantics/restrictedAccess |
Aparece en las colecciones: | Ingeniería Mecánica |
Ficheros en este ítem:
Fichero | Descripción | Tamaño | Formato | |
---|---|---|---|---|
bellido_eg.pdf | 21,61 MB | Adobe PDF | Visualizar/Abrir |
Este ítem está sujeto a una licencia Creative Commons Licencia Creative Commons
Indexado por:
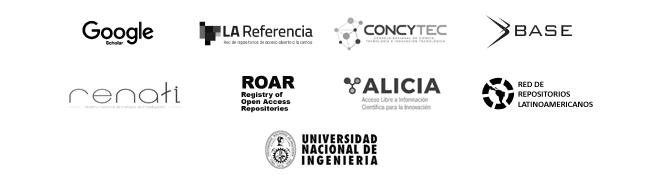